How can we help?
Manage Metric Definitions and Targets
Metric Definitions
The Metric Definitions screen allows each customer to fine tune the calculations used for some standard metrics. The calculation is shown in bold within each Metric section, then specifics can be specified altering the definition of some of the variables within the calculation.
Utilization
The calculation for Utilization is:
Utilization = Actual Run Time / Total Time
The definition of Actual Run Time and Total Time can be specified using the check boxes.
Default Cycle Status for Actual Run Time: Scytec DataXchange supports the use of multiple definitions for Cycle Time. Either the General In Cycle definition can be used or a combination of Specific In Cycle statuses can be selected.
Use Defined Shift as Total Time: Setting this option to True uses the defined shifts for the calculation of total time. The Defined Shift as Total time is intended to be used when a planned downtime is entered by the operator during the shift, and non-shift hours are recorded as Unknown Downtime.
Subtract Planned Downtime from Total Time: Select the Planned Downtimes that should be excluded from the Total Time in the Utilization calculation. Select General Planned Downtime to exclude all Planned Downtime statuses.
Subtract Unplanned Downtime from Total Time: Select the Unplanned Downtimes that should be excluded from the Total Time in the Utilization calculation. Select General Unplanned Downtime to exclude all Unplanned Downtime statuses.
Subtract Unknown Downtime from Total Time: Setting this option to true subtracts any unknown downtime that has occurred from the total time.
Unexpected Utilization Values
With some settings, it is possible for Utilization to exceed 100% or be less than 0%. If Use Defined Shift as Total Time is enabled, and the machine runs outside of shift hours, a Utilization value exceeding 100% can occur. Combining that setting with subtracting Downtimes from Total Time if the amount of downtime exceeds the shift time a negative Utilization value may be reported.
OEE (Overall Equipment Effectiveness)
Details on the OEE calculations can be found on the OEE Calculations page.
Use Defined Shift as Total Time: Setting this option to True will use the current defined shift time to calculate the total time.
Limit Performance to 100%: Setting this option to True will cause any OEE values exceeding 100% to be reported as 100%.
Treat Unknown Downtime as Unplanned: Setting this option to True will add Unknown Downtime to the Unplanned Downtime value for OEE calculations.
Additional OEE information
With Expressions, it is possible to automatically define downtime outside of a shift as a planned downtime such as ‘No Shift’ instead of using ‘Unknown downtime’. This can cause some unexpected results.
The “Subtract Planned Downtime from Total Time” option is intended to be used when planned downtime are entered by the operator during the shift, and non-shift hours are recorded as Unknown Downtime.
If the non-shift hours are already being converted to a planned downtime, when using shift times as total time and subtracting planned downtime from the total time the planned downtime during non-shift hours is being taken out twice.
There are two ways to solve this. If both items are set to true on the Manage form as it is was initially then you must select the Shift filter when running the chart.
The other solution is to set “Use Defined Shift as Total Time” to False since this time is already being accounted for as Planned Downtime. This is the recommended solution.
Parts Per Hour
Planned Downtimes to Exclude From Calculation: Allows you to remove the selected Planned Downtime from the parts per hour calculation.
Display As: Allows you to set the Ideal operation time for parts to display in minutes or hours.
Setup Times
Allows you to mark Planned Downtimes or Unplanned Downtimes as Setup Times for calculation of Actual Setup Time. The Actual Setup Time calculation will be the amount of downtime that has occurred based on the downtimes marked as Setup Times. Downtimes marked as Setup Times will be considered productive time for the purposes of OEE.
Metric Targets
The Metric Targets form allows for the configuration of target values and colors for each individual Metric. Use the check boxes to select the appropriate equipment then set the desired value within the associated sections to modify the values as desired.
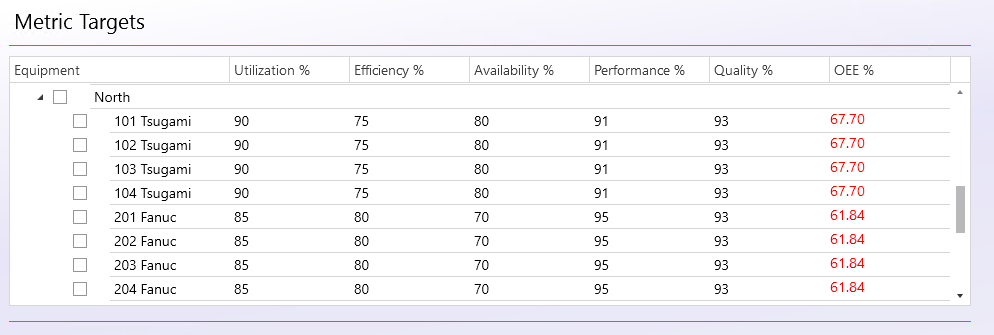
Utilization
By filling in the Utilization % and pressing the Enter button the desired utilization target percentage can be set for each piece of equipment selected along with setting the colors that will be used in the charts.
- Target: The color that will be used for the value specified on this page.
- On Target: The color that will be used if the actual value is within or above the specific target range.
- Below Target: The color that will be used if the actual value is below the specific target range.
- Off Target: The color that will be used if the actual value is lower than the Below Target range.
The percentages which set the limits for the different levels are defined on the filter page for the Utilization charts.
Efficiency
Efficiency % defines the expected percentage of Parts Per Hour the machine will actually produce. An Efficiency % value will modify PPH, PPH %, and Ideal Operation Time in all relevant Charts and Reports, as well as the RTV and ODI.